RMA is an abbreviation of ‘Return Merchandise Authorization’. It describes the process of a customer returning an item to either get a refund, have the product exchanged, or have the item repaired.
The way many companies handle RMAs.
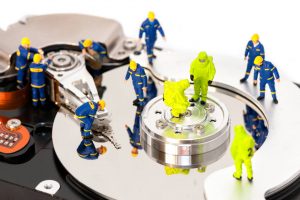
Handling RMAs correctly and fast is essential for the satisfaction of your customer.
RMA management in companies is often a necessary evil. Returned goods are not something you want, but it most likely occurs anyway, either due to a product defect, faulty delivery, or the like.
The process of managing RMA cases in a company is often very time-consuming. Therefore it’s often put aside in favor of the more ‘value-adding’ company tasks. We prioritize our daily main-tasks, and when the end of the day comes, there are just a few more item’s added to the list of RMAs that you’ll need to look at this when there is time.
That time is never there, and as you struggle to keep down that list of RMAs, it becomes harder and harder to keep that overview. It is difficult to remember all the details related to each item.
The documentation for an RMA may be insufficient, and you do not know what to do with the items on the shelf. Is the product defective in any way, or can we take it back to the warehouse? Who should credit the goods? Have the customer received a replacement/replacement? Should the product be returned to the supplier for repair? The questions can be many.
The above scenarios can lead to cases falling between two chairs. Suddenly the customer jerks for an answer to the RMA-case, and we rush to handle the issue in a hurry, with the risk of overseeing something or making some mistake. This hasty processing can cause inventories not to match and customers not being adequately compensated for their returns. The returns risk not undergoing the necessary checks before returning to the warehouse. When the customer subsequently contacts the company, there may be doubts about the course of events, with which misunderstandings may arise.
Best practice of managing and processing RMAs?
Working with RMA numbers and traceability is Alpha and Omega when handling returned goods/repairs. When the customer contacts the company regarding a return, it’s important to register this and give the customer a return number (RMA number) as well as an option to state, in a structured way, for example, order no., serial no., product no. as well as the reason for the return. When the product then arrives, we need to register it, and at this point, we have it under control and can quickly identify what it is and the reason for the return. The above way of work helps in processing the RMA further in the company.
If the product is defective, the customer will have written a more or less accurate problem description, which helps to quickly clarify whether we need to repair the product or whether we need to exchange it for a new product. If the customer returns the product due to a misplaced purchase or similar, we must check and test it BEFORE replacing it on the shelf for another customer to buy. We may need to forward the product to our supplier for replacement/repair. Here we must keep track of the product to a supplier. No matter what, we significantly benefit when we have documented all the steps in the RMA processing.
Today, many companies handle this documentation via spreadsheets or the like. This method might be sufficient and can meet the requirements required by ISO 9001 / ISO 13485. However, this method is a time-consuming job and rarely very effective. There is an increased risk of mistakes and a risk that the overview will be insufficient.
How Wismatix QMS can help you
A better method is to let a database system handle the RMA-cases. This method highly reduces the risk of mistakes while always maintaining an excellent overview, regardless of the number of cases. You will also have far better opportunities to compile statistics so that you can use this knowledge to reduce the number of RMA returns in the future.
At Wismatix, we have many years of practical experience setting up processes for easy handling of returned goods and repairs. We have integrated this experience in the RMA module of Wismatix QMS. With this module, you get a return management tool that works even on a busy day and ensures full traceability and statistics. You can use the statistics to reduce the number of returned items in the future, thereby saving time, improving customer satisfaction, and minimizing the company’s return costs.
Read more about what Wismatix QMS can help your company with here.